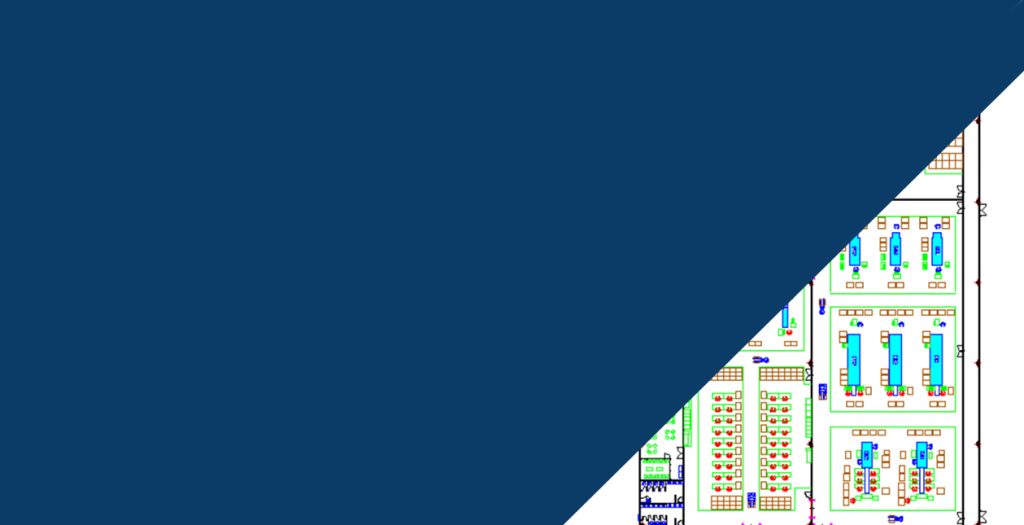
「11の工場建設実績を持つ現役コンサルタントが教える」
「工場レイアウト設計のプロが教える現場の生産性を30%向上させる配置術」
生産効率の向上・コスト削減・省スペース化を同時に
実現する実践的な工場レイアウト最適化メソッド」
「製造業が直面する工場レイアウトの5つの課題」
「あなたの工場でも、これらの問題が生産性を阻害していませんか?」
- 生産効率の低下とボトルネックの発生:
「工程間の連携不足や不適切な設備配置により、生産性が低下しています。
社員は懸命に働いているのに、なぜか目標生産数に届かない。
そんな状況は、多くの場合レイアウトに原因があるのです。」 - 過剰な在庫スペースによるコスト増加:
「中間在庫や仕掛品のための余分なスペースが経費を圧迫しています。
工場面積の20〜30%が実は非効率な在庫保管に使われている場合も。
これは毎月の家賃や設備維持費として直接コストに影響します。」 - 複雑な動線による作業効率の悪化:
「人・物・情報の流れが非効率で、無駄な動きが多発しています。
作業者が1日に歩く距離は平均3〜5km。
この移動時間は純粋な無駄であり、動線の最適化で解消できる課題です。」 - レイアウト変更時の生産停止リスク:
「効率化を図りたいが、長期の生産停止は避けたい。
多くの経営者がこのジレンマに直面しています。
改善のために生産を止めることはさらなる損失を生むと考え、
非効率なまま操業を続ける悪循環に陥っています。」 - 拡張・縮小への柔軟性不足:
「将来の需要変動や生産品目の変更に対応できないレイアウト。
一度設計したレイアウトが将来の変化に対応できず、数年後に大規模な改修が必要になるケースが頻発しています。」
「11の工場建設と数十件のレイアウト改善実績」
「印刷工場・ディスク製造工場・配送センターの専門知識で成果を実現」
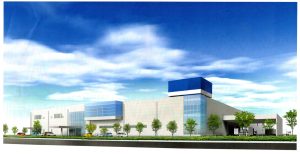
印刷工場
成果:
- 段取り替え時間65%削減
- 生産性38%向上
- 不良率22%低減
課題:
- 多品種小ロット生産による頻繁な版替え
- 工程間の複雑な仕掛品動線
- 納期短縮要求への対応遅れ
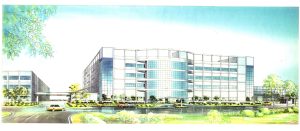
ディスク製造工場
成果:
- クリーンルーム有効活用率55%向上
- 品質不良率17%低減
- エネルギーコスト28%削減
課題:
- 高額なクリーンルームスペースの非効率な活用
- 複雑な製造工程と頻繁な品種切替
- クリーン度の維持と生産効率の両立
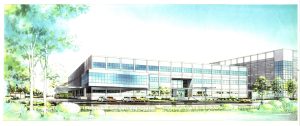
配送センター
成果:
- ピッキング効率42%向上
- 出荷ミス85%減少
- 床面積利用効率35%改善
課題:
- EC需要増加による急激な取扱量拡大
- 季節変動と多品種小口化への対応
- 既存設備内での処理能力向上要求
「失敗しない工場レイアウト設計の5つの原則」
- 物の流れを優先:
「製品の製造工程に沿った一方向の動線設計が基本です。原材料の入荷から製品の出荷まで、逆流や交差を最小限に抑えることで、混乱やミスを防ぎます。特に高頻度で移動する物の動線を最短にすることで、全体効率が大きく向上します。」
「詳細を読む」 - 柔軟性の確保:
「将来の変化に対応できる拡張性設計が重要です。生産量の増減や新製品の導入を考慮し、固定設備の配置を最小限にとどめ、モジュール式の生産セルを採用。将来の変更コストを最小化します。」
「詳細を読む」 - ボトルネック分析:
「制約工程を中心に全体最適を設計するアプローチです。TOC(制約理論)に基づき、生産性を律速している工程を特定し、その工程を中心にレイアウトを組み立てます。全体の流れはボトルネック工程の能力以上にはならないため、その最適化が最重要です。」
「詳細を読む」 - 5S活動との連携:
「整理・整頓・清掃・清潔・しつけを促進するレイアウト設計が成功の鍵です。必要なものがすぐに取り出せる収納スペース、清掃がしやすい通路幅、視覚管理がしやすい配置など、5S活動を組み込んだレイアウトは長期的な効率向上につながります。」
「詳細を読む」 - データ駆動設計:
「数値分析に基づく科学的アプローチが必須です。感覚や経験だけでなく、実際の生産データ、動作分析、シミュレーション結果に基づいてレイアウトを決定します。特に「スパゲティ図」を用いた動線分析は、無駄な移動を可視化する強力なツールです。」
「詳細を読む」
「あなたの工場に最適なソリューション」
「目的と予算に合わせた4段階のサービス」
無料オンラインメールセミナー
価 格: ¥0
詳 細:
工場レイアウト設計手法を10回のステップメール受講により、設計手法の
概要が理解できます。
無料の特典がダウンロードできます。
含まれるもの:
「工場レイアウト」設計の手法フロー図
基本レイアウト案の評価リスト
工場詳細レイアウト図の作図方法
相互関連図の作成ワークシート
設備投資額の経済計算
設備投資額の経済計算ワークシー
無料工場レイアウト診断:
価 格: ¥0
詳 細:
工場レイアウトの現状を自己診断できるチェックシートを無料でご提供します。
25の質問に答えるだけで、あなたの工場の改善ポイントが明確になります。
また、メールでの初期相談にも対応。最初の一歩としてリスクなく始められます。」
含まれるもの:
セルフチェックシート(PDF)
自動改善ポイント診断レポート
初回メールサポート(質問1回分)
オンライン相談:
価 格: ¥50,000〜
詳 細:
「Zoomを使った60分のオンライン相談で、工場の具体的な課題と改善策を
専門家が診断します。
工場の図面や写真をもとに、具体的な改善提案と簡易レイアウト図を作成。
費用対効果の高い改善策を提案します。
含まれるもの:
60分のZoomビデオ相談
現状分析と具体的改善提案書
簡易レイアウト図作成(1案)
フォローアップメール相談(2回分)
フルコンサルティング:
価 格: 打合せにより見積書を提出させていただきます。
詳 細:
「現地調査から実装サポートまで、工場レイアウト最適化の全工程をサポートします。
詳細な現状分析、複数のレイアウト案の作成と比較検討、2D図面の作成、移行計画の立案まで、一貫したサービスを提供。
生産性向上とコスト削減を確実に実現します。」
含まれるもの:
現地調査(1〜2日)
詳細なデータ分析レポート
複数レイアウト案の作成と2Dモデリング
費用対効果シミュレーション
段階的移行計画の立案
実装時のサポート(3回分の訪問)
「工場レイアウト最適化の4ステップ」
現状分析:
「まず現状を正確に把握することから始めます。
生産データの収集、工程間の関係性の分析、作業者の動線追跡、ボトルネック工程の特定などを実施。
客観的なデータに基づく分析が、効果的な改善の第一歩です。
この段階で、5S状況、在庫量、設備稼働率なども評価し、総合的な現状把握を行います。」
問題特定:
「収集したデータをもとに、非効率要因を見える化します。
スパゲティ図による動線の可視化、付加価値分析による無駄の特定、工程間のバランス分析などを通じて、具体的な問題点を洗い出します。
そして、投資対効果の観点から改善の優先順位を決定します。」
改善設計:
「特定された問題点を解決する最適レイアウトを設計します。
複数の改善案を作成し、それぞれについてシミュレーションを実施。
生産性、効率性、柔軟性、投資対効果などの観点から最適案を選定します。
必要に応じて3Dモデルを作成し、空間の有効活用や作業者の動線を視覚的に確認します。」
実装サポート:
「設計したレイアウトを現場に実装するための段階的な移行計画を立案します。生産停止時間を最小化するための週末作業や段階的移行のスケジュールを策定。設備移設の順序や一時的な仮設ラインの設置など、実務的な観点からの計画を立て、実装をサポートします。実装後の評価と微調整も行い、期待通りの効果が得られるようフォローアップします。」
特 典
Eブック
「工場レイアウト改善チェックリスト50」:
「生産性向上のために確認すべき50のポイントを網羅したチェックリストです。
現場ですぐに活用できる実践的な内容を凝縮。PDFでダウンロードでき、印刷して現場で使用できます。」
メルマガ「毎週のレイアウト改善ヒント」:
「毎週火曜日に配信される工場レイアウト改善のヒントメールマガジン。
実践的なテクニック、最新の業界動向、Q&A、成功事例など、継続
「工場レイアウトについてよくある質問」
- Q: 工場レイアウト変更にかかる期間はどのくらい?
A: 「工場の規模や複雑さによって異なりますが、典型的には計画段階に2〜4週間、実際のレイアウト変更の実施に1〜2週間程度かかります。ただし、大規模な工場や、特殊な設備がある場合はさらに時間がかかることもあります。当社では、生産への影響を最小限に抑えるため、週末や計画停止期間を利用した段階的な実施計画を立案します。」 - Q: 生産を止めずにレイアウト変更はできる?
A: 「多くの場合、完全に生産を止めることなく、段階的なレイアウト変更が可能です。週末作業の活用、一時的な仮設ラインの構築、夜間・休日の移設作業など、様々な手法を組み合わせることで、生産への影響を最小化できます。当社の実績では、通常操業の90%以上を維持しながらレイアウト変更を実施した事例が多数あります。」 - Q: 小規模工場でも効果はある?
A: 「はい、むしろ小規模工場の方が効果を実感しやすいケースが多いです。従業員30名以下の工場でも、適切なレイアウト改善により、生産性20〜40%向上、在庫スペース30〜50%削減などの効果が得られています。小規模工場は意思決定が早く、全体を俯瞰しやすいため、変更の実施がスムーズに進むことも利点です。」 - Q: コスト削減効果はどのくらい期待できる?
A: 「適切なレイアウト最適化により、一般的には総運営コストの15〜25%程度の削減が期待できます。具体的には、人件費(無駄な移動や作業の削減)、スペースコスト(有効活用による削減)、在庫コスト(仕掛品・中間在庫の削減)、エネルギーコスト(効率的な設備配置)などが主な削減項目です。投資回収期間は通常6ヶ月〜1.5年程度となっています。」 - Q: どんな業種に対応できる?
A: 「機械加工、電子部品製造、自動車部品、物流倉庫、印刷業など、幅広い製造業に対応可能です。業種固有の要件(クリーンルーム要件、重量物の取り扱いなど)にも精通しており、それぞれの業界特有の課題に対応したレイアウト設計を提供します。これまで11の異なる業種で実績があります。」
「まずは無料診断から始めませんか?」
「工場の生産性を今すぐ向上させるための第一歩を踏み出しましょう。
当社の無料診断シートは、わずか5分の入力で、あなたの工場の隠れた可能性と改善ポイントを発見できる強力なツールです。
診断結果は即時にEメールでお届けします。
製造業20年の経験から開発された診断方法で、生産性向上の可能性を数値化。
どの領域に最も大きな改善余地があるのかを明確に示します。
すでに110社以上の製造業がこの診断シートを活用し、平均30%の生産性向上に成功しています。
あなたの工場も、最適なレイアウトで本来の力を発揮しませんか?」
- 「診断は完全無料、購入義務はありません」
- 「個人情報は厳重に保護し、営業目的での連絡はいたしません」
- 「すぐに実践できる改善ヒント付きレポートを即日お届けします」
会社情報
- 「工場レイアウト情報室」
- 「製造業の生産性向上を支援する専門コンサルティング」
- 「〒425-004 静岡県焼津市坂本262-1」
- 「TEL: 080-4205-7704
- 「E-mail: galaxy@ny.tokai.or.jp」
おすすめの記事コンテンツ
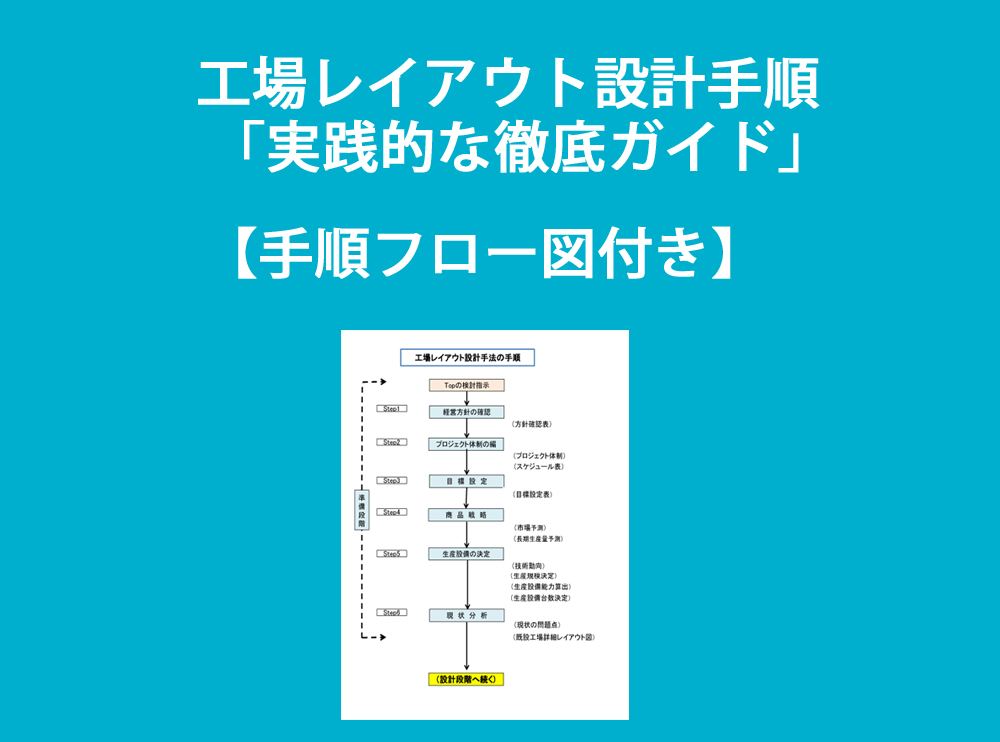