代替ブロックレイアウト案の作成の重要性
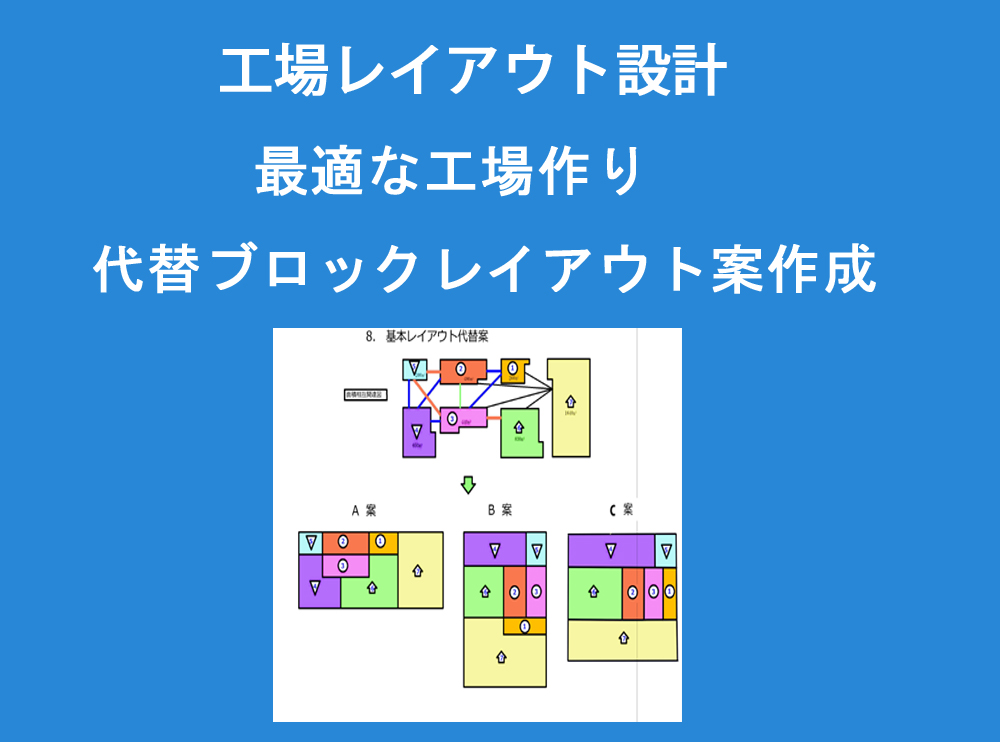
工場レイアウト設計における代替ブロックレイアウト案の作成の重要性
〜最適な工場づくりのために必要な「ひと手間」〜
要 約
代替案があるかないかで、レイアウトの質は大きく変わる
工場のレイアウトを考える際、「ブロックレイアウト図」を作成するのは非常に大きなステップです。
配置がまとまり、図面に落とし込まれると、なんとなく完成した気がしてしまうかもしれません。
しかし、そこで満足してしまっては本当にもったいないのです。
なぜなら、最初の案が必ずしもベストとは限らないからです。
実際の現場では、材料の流れ、作業者の動線、機械のメンテナンススペース、将来の増設計画、さらには建設コストや安全面まで、多様な要素が絡んできます。
どんなに優れた案でも、何かしらのトレードオフ(あちらを立てればこちらが立たず)が生まれるのが普通です。
だからこそ、「この案が正解だ」と思う前に、いくつかの代替案を作って比較検討することが不可欠なのです。
読者の皆さんへ:こんな方に読んでほしい内容です
この記事は、以下のような悩みをお持ちの方に向けて書いています。
- 工場レイアウト設計をこれから始めるが、何から手をつければいいのか分からない方
- 何となくレイアウト案はできたものの、「本当にこれでいいのか」と不安を感じている方
- 計画が停滞しており、打開策を見つけたいと考えている方
- 上司や経営層との合意がうまく取れず、提案に説得力を持たせたい方
これからお伝えする内容を理解・実践することで、以下のような成果が得られます:
- 設計プロセスの中で、どこに注力すべきかが明確になります
- 失敗しがちなパターンを事前に回避する力がつきます
- 他者との合意形成がスムーズになり、計画が前に進みやすくなります
ブロックレイアウト図作成の位置づけ
工場レイアウトの設計には、段階的なステップがあります。
ヒアリング・要件整理・ゾーニングを経て、設計段階のStep6で「ブロックレイアウト図の作成」に至ります。
この段階では、エリアごとの大まかな配置を視覚化し、「どういう構造の工場になるのか」という骨格を固めていきます。
例えば、以下のような内容が明確になります:
- 生産ラインと搬出入口の位置関係
- 倉庫や事務所の配置バランス
- 通路の取り方や搬送機器の動線
このブロック図を元に、次の段階で設備や機器の具体的なレイアウト(詳細レイアウト)へと落とし込んでいきます。
ですので、この段階の判断が後工程に大きく影響するのは言うまでもありません。
これが工場レイアウト設計の設計段階Step7になります。
次図にその位置を示します。
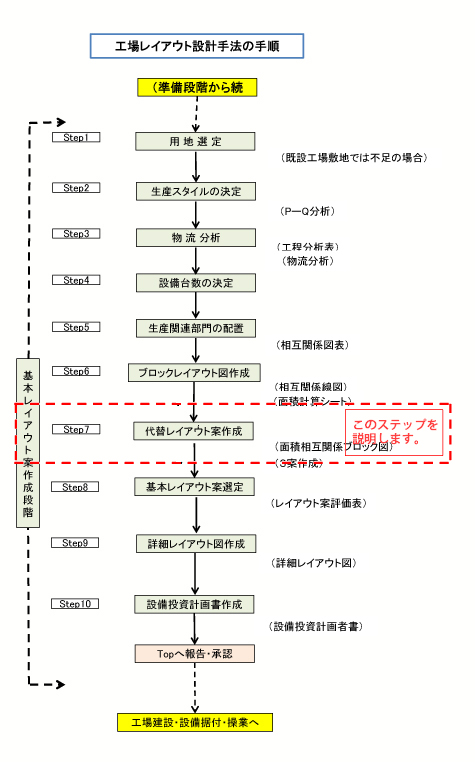
なぜ「代替案」を作るべきなのか?
1. 最初の案に「思い込み」が含まれていることも
初めて作成したブロックレイアウト案は、ある意味「思いつき」や「先入観」に基づいているケースも少なくありません。
設計者の頭の中にあるイメージをそのまま形にしただけ、ということもあるのです。
しかし、レイアウト設計は「多角的な視点」から考えることが重要です。
- 物流のスムーズさ
- 作業者のストレス軽減
- 安全性の確保
- スペースの有効活用
- コストの最小化
- メンテナンスのしやすさ
- 将来の拡張性
これらをすべて1案で満たすのは簡単ではありません。
だからこそ、視点を切り替えて別の案を考えることが不可欠になります。
2. プロジェクト関係者との「対話」がしやすくなる
工場の設計は、設計者一人で完結するものではありません。
実際に使うのは現場の作業者であり、経営者は投資判断を、物流担当者は効率を、安全担当者は法令や事故リスクを気にします。
このとき、「この案しかありません」と1つの案を出されても、相手は不安を感じます。
「本当に他に良い方法はないのか?」と疑問を持つのは当然です。
逆に、複数の案を並べて比較できれば…
- 「A案は物流が最短、B案は人の動きがスムーズ」
- 「C案は増設が簡単、D案は現状設備の活用ができる」
と、共通の土俵で対話ができるようになります。
これは、設計案への納得感を生むだけでなく、チームとして意思決定を進めるうえで非常に有効なアプローチです。
このように、「代替案をつくる」という行為は、ただの作業の繰り返しではありません。
それは、**より良い案を導くための「思考の広がり」**であり、設計者としての成熟度を高めるステップでもあります。
実践編:代替ブロックレイアウト案の作成手順と考え方
ここからは、代替案を「どうやって作るか?」をテーマに、具体的な方法や思考のコツをお伝えします。
理屈だけでなく、誰でも実践できるように、段階を追って説明していきます。
1. 「視点を変える」ことから始めよう
代替案を作る第一歩は、「別の見方で考える」ことです。
最初の案は、どうしても自分の慣れた思考や、あるひとつの優先軸から構成されがちです。
ここで大切なのは、目的を明確にしてテーマを分けることです。
以下のような視点の切り替えが非常に効果的です。
◆ 物流効率を最優先した案
材料の搬入から製品の出荷まで、最も短い距離・最少の工程で完結できる配置を考えます。
無駄な折り返しや横断を排除し、フォークリフトなどの動きも最小にします。
◆ 作業者の動きやすさを重視した案
人の動線を短く、交差のないスムーズな流れにします。
特に手作業が多い職場では、疲労やヒューマンエラーを防ぐために動きやすさは重要です。
◆ 拡張性を重視した案
将来、新たな生産ラインや設備を増設する予定がある場合、そのスペースや動線を確保しておく設計です。
今だけでなく5年先、10年先を見据える目線が必要です。
◆ コストを最小に抑える案
既存の建物や設備、配管を極力そのまま活用するなど、初期投資を減らす方向で考える案です。
リニューアル案件や予算が限られたプロジェクトでは特に重要です。
◆ 安全性を最優先にした案
作業者とフォークリフトの通路を完全に分離したり、非常時の避難ルートを明確に確保した配置など、安全管理の視点から設計します。
2. テーマごとに案を描いてみよう(手描きでもOK)
テーマが決まったら、それぞれの視点で**ブロック図(エリア配置のラフ図)**を作ってみましょう。
パソコンを使うのも良いですが、最初は手描きでも十分です。
✅ ヒント:
- 四角いブロックで「エリア」を描き、色分けして目的別に見やすく
- 矢印を使って「物流」や「人の動き」の方向を示す
- 複数案をA案・B案・C案…と分けて並べる
ここでは「正解を描く」のではなく、「あえて違う視点から構成してみる」ことが目的です。
「無理に違うことをやろう」と思うぐらいで、ちょうどいいです。
次図がその事例です。
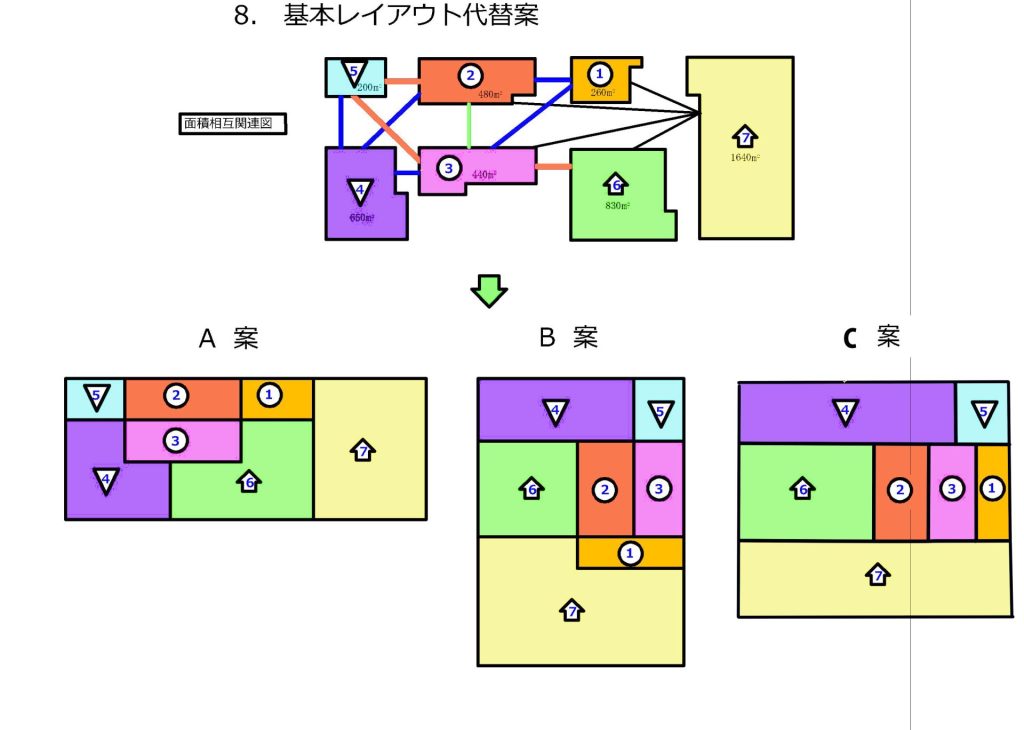
3. 案を評価・比較する
複数の案ができたら、次は比較して良し悪しを客観的に把握していきます。
このとき、以下のような表を使って評価するのが効果的です。
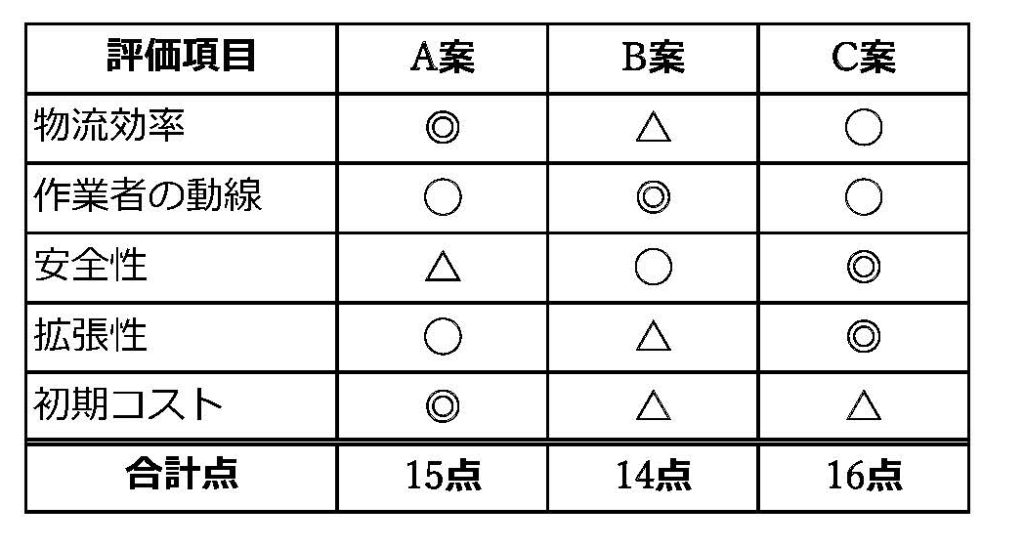
✅ ヒント:
評価は「◎」「◯」「△」の3段階でよく、点数をつける場合は5点満点でもOK。
評価基準は、関係者と相談して決めておくと、議論がスムーズになります。
この表を使うことで、「なんとなく良さそう」ではなく、論理的な比較ができるようになります。
また、複数の案の「良いところ取り」をして、ハイブリッド案を作ることも可能です。
4. プロジェクト関係者との意見交換の場を持つ
案を作ったら、それをプロジェクト関係者(ステークホルダー)に提示して、意見を聞いてみましょう。
ここで重要なのは「相手の立場で考えること」です。
たとえば:
- 現場作業者は動線や作業のしやすさを重視
- 経営層は費用対効果や拡張性を重視
- 安全管理者は通路の交差や非常口の配置を重視
こうした複数の視点を取り入れることで、実用的で納得感のあるレイアウトが見えてきます。
一人で考えるよりも、チームの知恵を使うことで、完成度は飛躍的に高まります。
5. 代替案がもたらす“気づき”と“進化”
複数案をつくっていると、意外な発見があります。
「A案だと思っていたけど、B案の方がメンテナンス性が良かった」
「C案の倉庫の位置、実は従業員の導線にも最適だった」
このように、比較することでしか見えてこないメリットや課題が浮かび上がるのです。
代替案は、ただ「選ぶ」ためだけのものではなく、設計を進化させる材料でもあります。
6. 実例から学ぶ:代替案が決定打になったプロジェクト
実際、私が関わったある製造工場の改修案件では、以下のような代替案の作成が功を奏しました。
- 当初案(A案):物流重視で、フォークリフトが一直線に走れる配置
- 代替案(B案):人の動線重視で、作業エリアの交差をゼロに
- 最終案:AとBを組み合わせたハイブリッド案で採用
現場の作業者と経営層、双方が納得し、結果として稼働開始からのトラブルもほぼゼロ。
「代替案を用意しておいて良かった」と心から思えたプロジェクトでした。
7. 「代替案づくり」を標準工程に組み込もう
これまで見てきたように、代替案は思いつきでやるものではなく、むしろ設計プロセスの一部としてルール化すべき工程です。
たとえば、設計フェーズのチェックリストにこのような項目を追加してみてください。
- □ 最低3案の代替ブロック案を作成したか?
- □ 各案の設計テーマ(物流、人、拡張、安全、コスト)を明確にしたか?
- □ 比較評価表に基づいて関係者と議論を行ったか?
- □ 最終案の選定理由をドキュメント化したか?
こうすることで、設計の質にバラつきがなくなり、再現性の高いプロセスになります。
プロジェクトが変わっても、チームが変わっても、同じレベルの成果を出すための仕組みになります。
8. AIやITツールの活用も視野に
最近では、ブロックレイアウト作成やレイアウト比較に活用できるITツールやAI支援ソフトも登場しています。
- 簡単なCADソフトで案を複製し、条件ごとに改変
- AIが動線や物流のシミュレーションを可視化
- クラウド共有で関係者と即時レビュー
人間の発想力と、デジタルの処理能力を組み合わせることで、スピーディかつ深い検討が可能になります。
代替案作成も、効率よく、しかも質を落とさずに行える時代になってきています。
代替レイアウト案の作成の概念は次図のようになります。
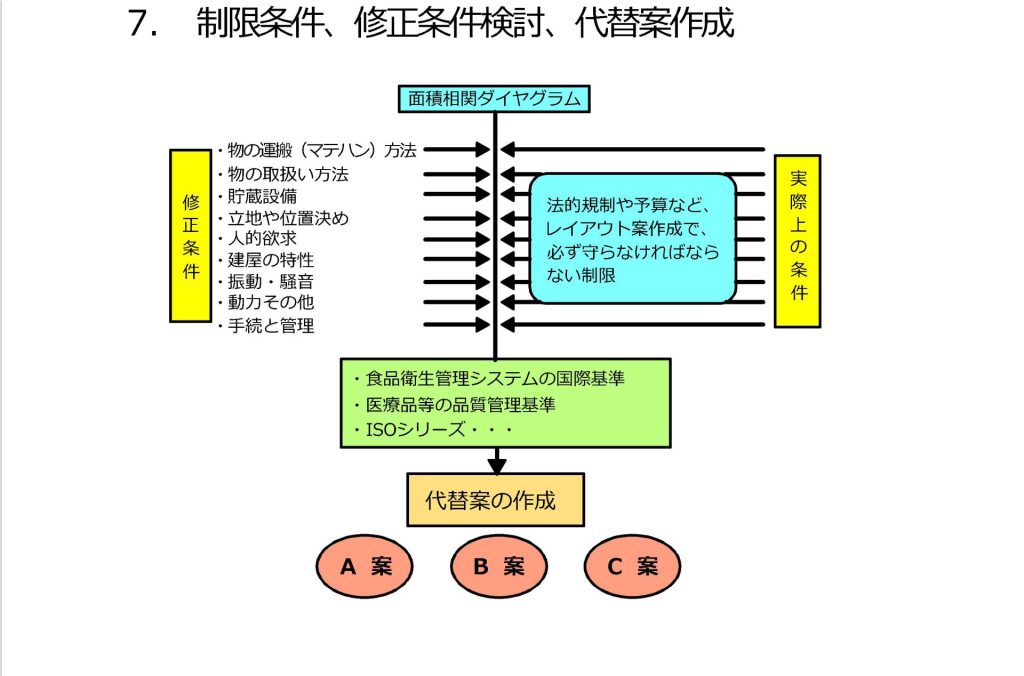
まとめ:
設計力の差は、案の“引き出し”で決まる
最初の案だけで進めてしまうと、「もしも」に対応できません。
逆に、複数案を検討する習慣がある設計者は、想定外にも強く、判断にも説得力があります。
「案を出せる人」=「設計の未来を切り開ける人」
それが、私がコンサルタントとして現場で感じてきた実感です。
あなたもぜひ、「代替案づくり」を日常の設計工程に取り入れてみてください。
代替案こそが設計の“引き出し”を増やす
一つの案だけでは“選べない”
- 視点を変えれば新たな価値が見える
- 複数案の提示はチームの信頼を得るカギ
- 比較評価によって論理的な判断が可能に
- 最適なレイアウトは、複数案の中に隠れている
代替案を作ることは、手間ではありません。
むしろそれは、設計の質を引き上げるために欠かせない“戦略”なのです。
参考
工場の新設や拡張や模様替えで、工場のレイアウトを考える必要が出てきた場合、まずは、下記の「やさしい工場レイアウト手法」のメール講座がおすすめです。
無料ですので、ぜひ活用してみてください。 ➡︎ 【無料】『やさしい工場レイアウト手法』メール講座