工場レイアウト設計における基本レイアウト案の選定の重要性
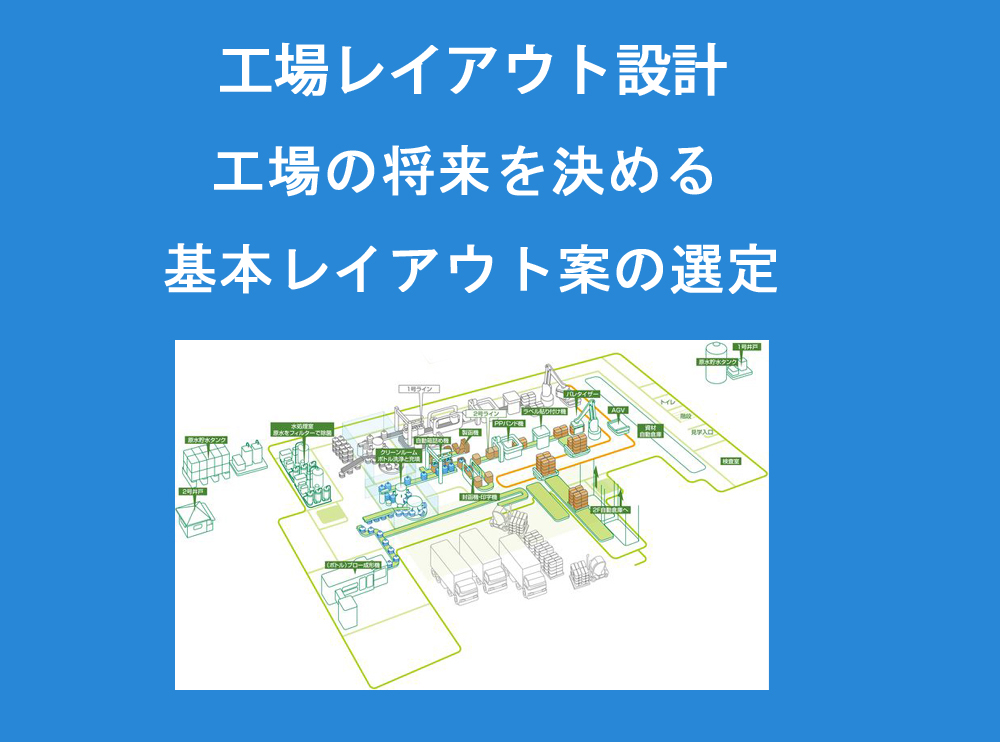
工場レイアウト設計における基本レイアウト案の選定の重要性
目次
はじめに:レイアウト案が出そろった、その先へ
前回の記事では、Step7として「代替ブロックレイアウト案の作成」について解説しました。
複数の案を出し、さまざまな視点から検討することで、最適な工場づくりへの道が開けてきます。
そして今回のテーマは、「基本レイアウト案の選定」です。
代替案を出したら、それをしっかり比較し、「これでいこう」と選び取る工程が必要です。
この「選ぶ」という行為が、設計の精度と工場の将来に大きな影響を与えます。
今回は、その重要性と実践的な進め方について、わかりやすく解説していきます。
読者の皆さんへ:こんな方に読んでほしい内容です
この記事は、以下のような悩みをお持ちの方に向けて書いています。
- 工場レイアウト設計をこれから始めるが、何から手をつければいいのか分からない方
- 何となくレイアウト案はできたものの、「本当にこれでいいのか」と不安を感じている方
- 計画が停滞しており、打開策を見つけたいと考えている方
- 上司や経営層との合意がうまく取れず、提案に説得力を持たせたい方
これからお伝えする内容を理解・実践することで、以下のような成果が得られます:
- 設計プロセスの中で、どこに注力すべきかが明確になります
- 失敗しがちなパターンを事前に回避する力がつきます
他者との合意形成がスムーズになり、計画が前に進みやすくなります
基本レイアウト案選定の位置づけ
工場レイアウトの設計には、段階的なステップがあります。
ヒアリング・要件整理・ゾーニングを経て、設計段階のStep7で「基本レイアウト案の選定」に至ります。
この段階では、3案の代替レイアウト案を比較、評価して、最適な基本レイアウト案を選定する非常に重要な作業になります。
例えば、以下のような内容が明確になります:
- 生産ラインと搬出入口の位置関係
- 倉庫や事務所の配置バランス
- 通路の取り方や搬送機器の動線
この基本レイアウト案を元に、次の段階で設備や機器の具体的なレイアウト(詳細レイアウト)へと落とし込んでいきます。
ですので、この段階の判断が後工程に大きく影響するのは言うまでもありません。
これが工場レイアウト設計の設計段階Step7になります。
次図にその位置を示します。
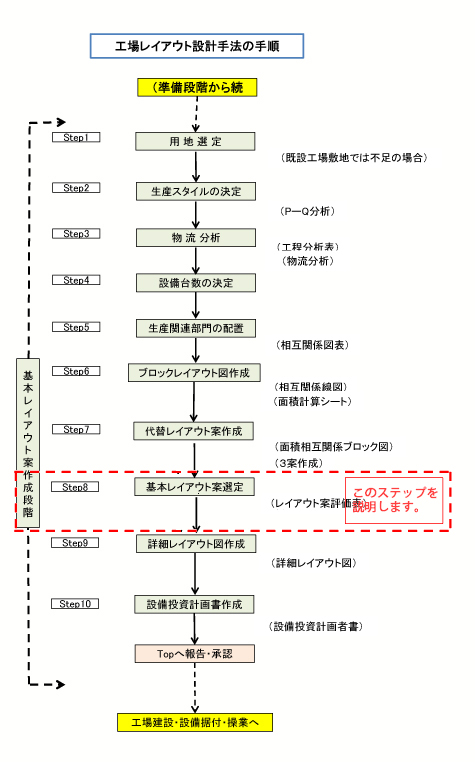
基本レイアウト案の選定は、設計の成否を分けるカギ
複数の案から最適なレイアウトを「選定する」ことは、単なる判断ではなく、工場の未来を方向付ける意思決定です。
ここであいまいな選び方をすると、後工程での修正やトラブルの原因になります。
逆に、しっかりと根拠をもって選んだレイアウト案は、その後の詳細設計・施工・運用にわたるまで、一貫した判断基準と
なり、ブレない工場設計を実現します。
選定が甘いと、設計プロジェクト全体が迷走する
選定が中途半端なまま進めると、関係者の意見がばらばらになり、工事が始まってから変更が発生することも少なくありません。
とくに、以下のような事態が起こりやすくなります:
- 経営層と現場の意見がすれ違い、調整が難航
- 設備業者や建築担当者との連携にズレが出る
- 「やっぱり別の案がよかった」となる二度手間・三度手間
- 最終的にコストや工期が増えてしまう
つまり、案を「出す」ことと同じくらい、「選ぶ」ことにこそ、慎重さと客観性が求められるのです。
具体例
比較と評価のステップを丁寧に進めよう
ステップ①:評価軸を明確にする
案を選定するには、まず評価の基準をそろえることが大切です。
以下のような観点をチームで共有しましょう:
- 物流効率
- 作業効率
- 安全性
- 拡張性
- コスト
- メンテナンス性
ステップ②:案を比較する
それぞれの案について、点数評価や◎◯△形式の表をつくると、関係者全員が同じ目線で検討しやすくなります。
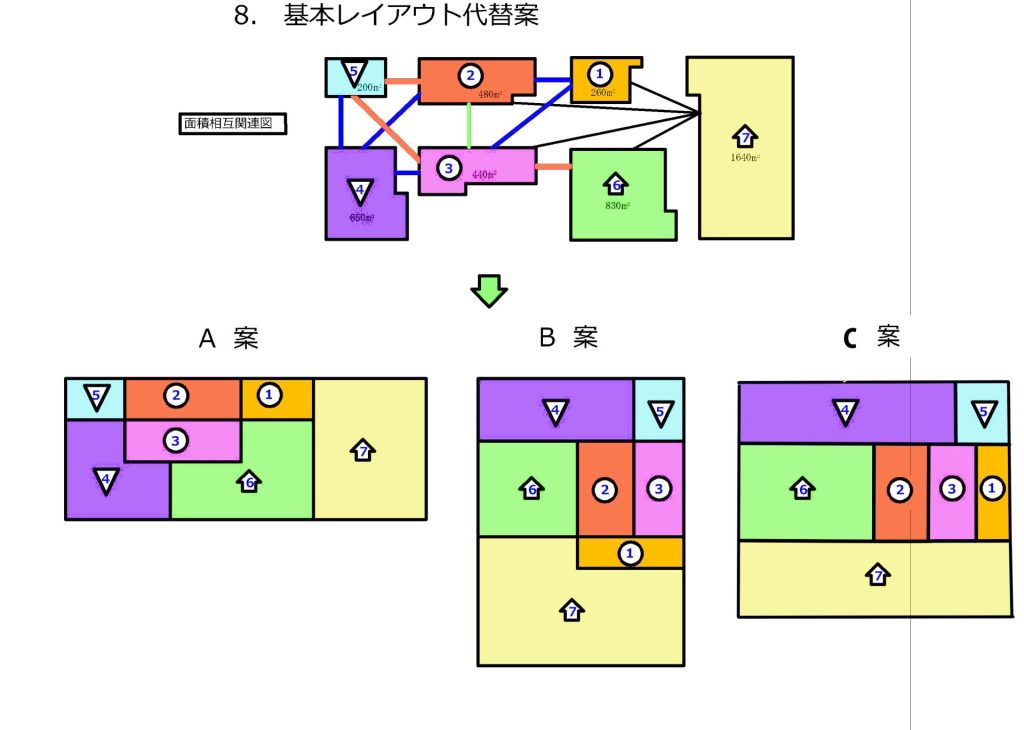
ステップ③:合意を得る場を設ける
「全員一致」よりも、「納得と説明責任」を大切に。
関係者が選定に関与した実感があるほど、後の設計もスムーズに進みます。
実例で学ぶ「選定」の成否
● 成功事例:S社の取り組み
3案をマトリクスで評価し、B案を選定。評価プロセスを文書化し、手戻りゼロで竣工。
現場の声:「設計に参加した実感があった」。
● 失敗事例:T社のトラブル
経営判断で案が即決。
結果、設備搬入で問題が発生し、後から大幅な変更と追加費用が発生。
→ 選定の軽視は、後の「高コスト化」につながる。
評価マトリクスを使って納得の選定を
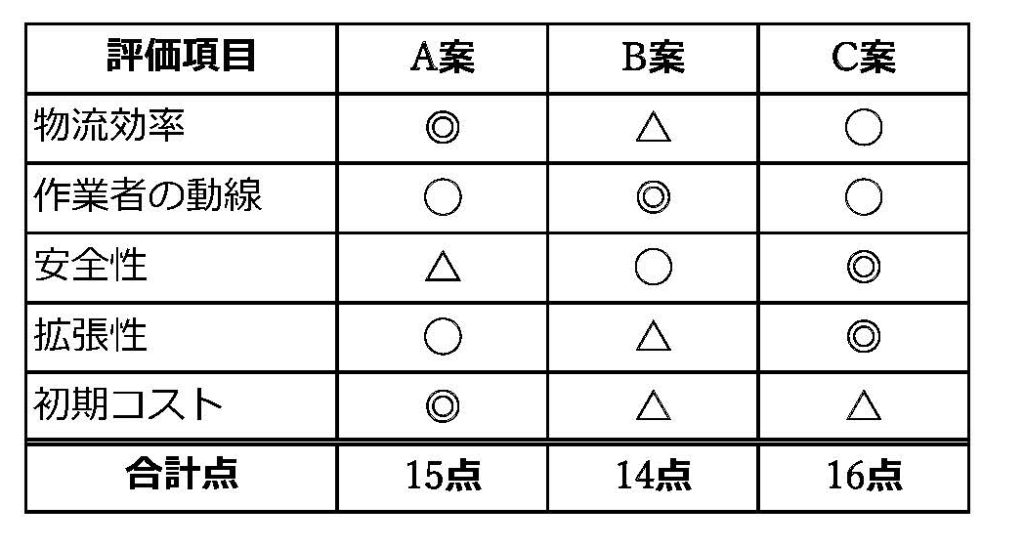
感覚で判断せず、見える化した情報で論理的に選ぶことが成功のカギです。
🔍 比較表の作成ポイント(より理解されやすくするために)
1. 評価基準の説明を加える
→ たとえば「生産性 = 生産量/作業時間」「従業員の満足度はアンケート結果で評価」など、どう点数を付けたかの基準
や定義を簡潔に補足しておくと、より信頼性が高まります。
2. 関係者でウエイト設定を共有する
→ ウエイト(重要度)を設定する際は、経営者・生産技術・現場担当者の複数視点で決めたことを明示すると、合意形成がしやすくなります。
3. 「視覚的な補助」も併用する
→ 同じ評価表でも、以下のような視覚補助を加えるとさらに伝わりやすくなります:
- 点数に色をつける(赤=低評価、青=高評価 など)
- 上位項目にアイコン(◎)を追加する
- 各案の特徴を吹き出しやグラフで補足
. よくある失敗とその回避ポイント
- 評価軸が曖昧 → 最初に重視項目を決める
- 多数決で決めてしまう → 議論の質と納得感を優先
- 選定理由を残していない → 設計変更時の判断に困る
ChatGPTのような支援ツールを活用しよう
AIツールは「選定の補助役」として優秀です。
以下のような用途で役立ちます:
- 案の評価軸を整理したいとき
- 関係者への説明文をまとめたいとき
- 意見が割れたときの整理役として
「思考の壁打ち」として活用することで、設計チームの質が一段上がります。
「選定力」を持つ設計者が信頼される理由
設計は「選ぶことの連続」です。
一歩ずつ選びながら、ゴールへ近づく──この地道な判断を積み重ねる力が、チームを導く設計者の資質です。
まとめ
読者のあなたへ:「選ぶ」ことから始めてみよう
今日からできる一歩:
- 複数案の比較表をつくる
- なぜこの案が良いか、説明文を考えてみる
- 他者の視点も取り入れて検討する
最後に:あなたの設計は「選択の積み重ね」
「代替案を出す」だけで終わらず、「どう選ぶか」こそがプロの領域です。
決断力のある設計者は、現場でも信頼されます。
参考
工場の新設や拡張や模様替えで、工場のレイアウトを考える必要が出てきた場合、まずは、下記の「やさしい工場レイアウト手法」のメール講座がおすすめです。
無料ですので、ぜひ活用してみてください。 ➡︎ 【無料】『やさしい工場レイアウト手法』メール講座