工場レイアウト設計:詳細レイアウト図で決まる将来の生産効率
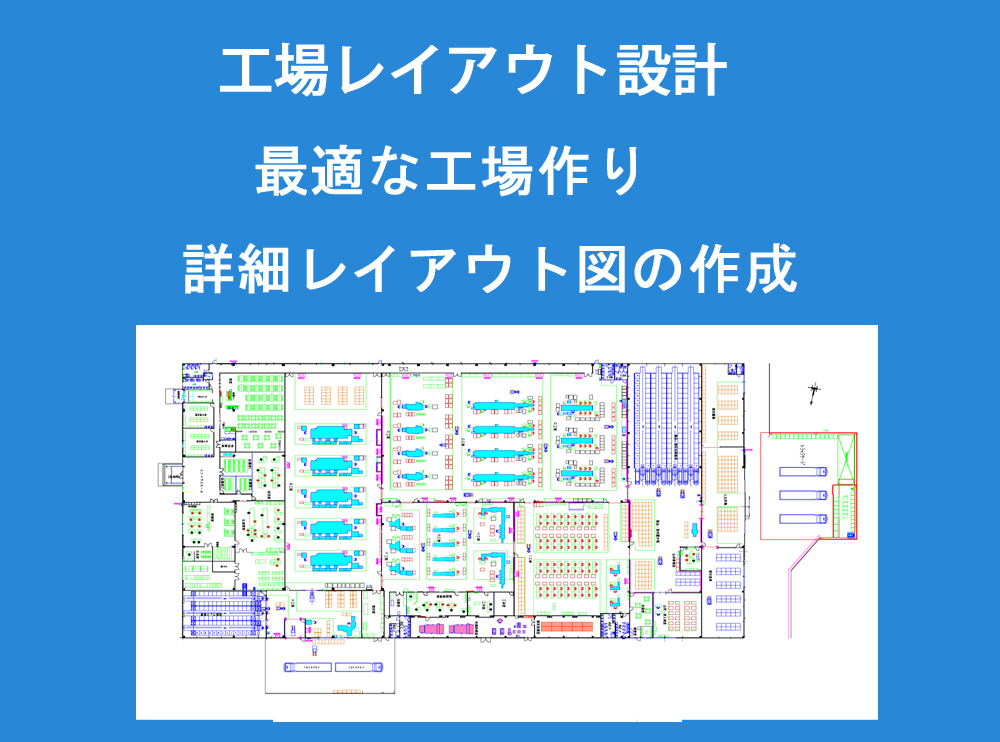
工場レイアウト設計:詳細レイアウト図で決まる将来の生産効率
目次
はじめに
基本レイアウト案が完成したら次にやること
工場レイアウト設計では、これまでに大まかな配置や動線を検討し、Step8で「基本レイアウト案の選定」までを終えました。
ここまでの段階では、工場内部の設備やスペースの配置の大枠が固まっているはずです。
しかし、実際に工場を稼働させるにあたっては、より詳細な情報を盛り込み、誰が見てもわかりやすく、運用しやすい「詳細レイアウト図」を完成させる必要があります。
この「詳細レイアウト図」は、工場の稼働における最終的な“設計図”ともいえます。
たとえば、機械や作業台のサイズ、保管する在庫の置き場、作業員の通路幅、人とフォークリフトなど車両の動線、安全設備の設置位置など、細かい部分を正確に描き込むことで、より具体的で実践的なレイアウト情報を共有できます。
今回は、工場レイアウト設計の初級から中級者の方に向けて、「詳細レイアウト図の作成」に焦点を当て、その重要性と作成時のポイントを解説します。
なお、本記事では詳しい図面作成の技術的な話よりも、
「なぜ詳細レイアウト図が重要なのか」
「どのように作成すればよいか」
など、実践的な視点を中心にお伝えします。
最後にはまとめも用意し、次のステップとしてどんな情報を知っておくとよいかもご紹介しますので、ぜひ最後までご覧ください。
読者の皆さんへ:こんな方に読んでほしい内容です
この記事は、以下のような悩みをお持ちの方に向けて書いています。
- 工場レイアウト設計をこれから始めるが、何から手をつければいいのか分からない方
- 何となくレイアウト案はできたものの、「本当にこれでいいのか」と不安を感じている方
- 計画が停滞しており、打開策を見つけたいと考えている方
- 上司や経営層との合意がうまく取れず、提案に説得力を持たせたい方
これからお伝えする内容を理解・実践することで、以下のような成果が得られます:
- 設計プロセスの中で、どこに注力すべきかが明確になります
- 失敗しがちなパターンを事前に回避する力がつきます
- 他者との合意形成がスムーズになり、計画が前に進みやすくなります
詳細レイアウト図作成の位置づけ
工場レイアウトの設計には、段階的なステップがあります。
ヒアリング・要件整理・ゾーニングを経て、設計段階のStep8で「基本レイアウト案の選定」に至ります。
この基本レイアウト案を元に、次の段階で設備や機器の具体的なレイアウト(詳細レイアウト)へと落とし込んでいきます。
ですので、この段階の判断が後工程に大きく影響するのは言うまでもありません。
これが工場レイアウト設計の設計段階Step9になります。
次図にその位置を示します。
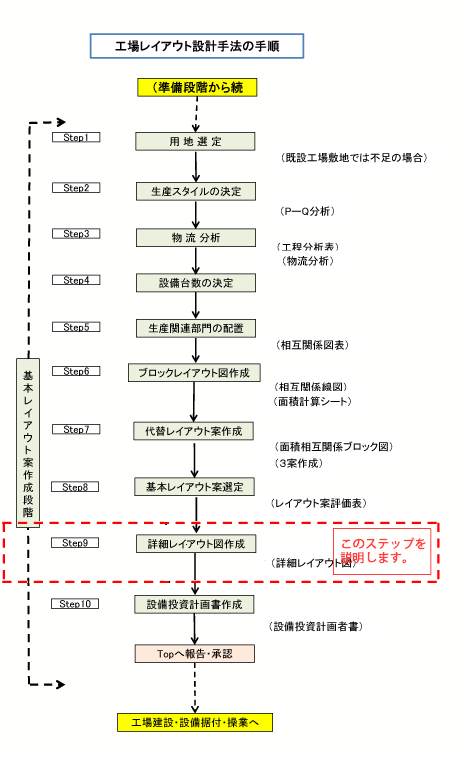
詳細レイアウト図作成の重要性
詳細レイアウト図は、工場の“実際の動き”を具体的に落とし込む最終段階の設計図であり、工場内の生産効率や安全性に直結する重要な要素です。
基本レイアウト案が示す大枠だけでは不十分であり、詳細レベルの情報を盛り込むことで、従業員が迷わない作業導線と生産性向上を実現できます。
工場計画の成功可否は、最後の最後に描かれるこの詳細図にかかっているといっても過言ではありません。
詳細レイアウト図作成の必要性
- 実際に稼働させるための最終判断材料
基本プランでは製造工程の流れや機械配置の概略を検討しますが、実際に機械を置く位置の数センチの違いや、棚の高さの違い、さらには消化器や立ち入り禁止区域の設定など、具体的に考慮すべきことは山ほどあります。
詳細レイアウト図をつくる段階で、これらを最終調整するわけです。
(2) トラブルやロスを未然に防ぐ
詳細レイアウト図がないまま工事や導入を進めると、いざ搬入時になって「機械が通らない」「作業スペースが確保できない」「検査工程で人が詰まる」といったトラブルが起きかねません。
描き込まれた詳細図を事前にチェックすることで、実際に起こりうる問題を洗い出し、修正できるのです。
(3) 現場とのスムーズな共有
工場レイアウトは、設計担当者だけでなく、実際に作業を行う現場のオペレーターやメンテナンス担当者とも情報を共有しなければなりません。
詳細レイアウト図がしっかりしていると、だれが見ても動線や設備位置が明確で、計画の意図が伝わりやすくなるため、導入時・稼働開始時の混乱を最小限に抑えることができます。
詳細レイアウト図に書き込む情報
たとえば、以下のような詳細情報をレイアウト図に落とし込みます。
・機械ごとの正確な占有スペースと安全柵の位置
・作業台や測定器、工具棚などの配置場所
・人の通路とフォークリフト、台車など車両が走行する通路を明確に区分
・原料や半製品、製品など在庫を置くパレットの数や保管場所
・消防設備や非常口、避難経路の表示場所
・照明やコンセント、配管ルート、配線経路などインフラ系の配置
・ISOや各種規格に基づく看板や標識の設置位置と内容
これらを正確に図面に記入すると、
「このスペースはメンテナンス用」
「このラインは人が乗らない」
「ここは危険区域なので安全柵が必要」
というように、現場作業者が具体的なイメージを持ちやすくなります。
たとえば、フォークリフト用の通路幅ひとつを取っても、通常では2メートルや3メートルなどこの程度でいいだろうと考えがちですが、実際には走行ラインの取り方や旋回スペース、積荷の大きさによって最適な幅は異なります。
詳細レイアウト図があるだけで、こうした微調整を事前に検討できるため、工場の運営開始後の修正コストやトラブルを大幅に削減できるでしょう。
次図が事例図です。
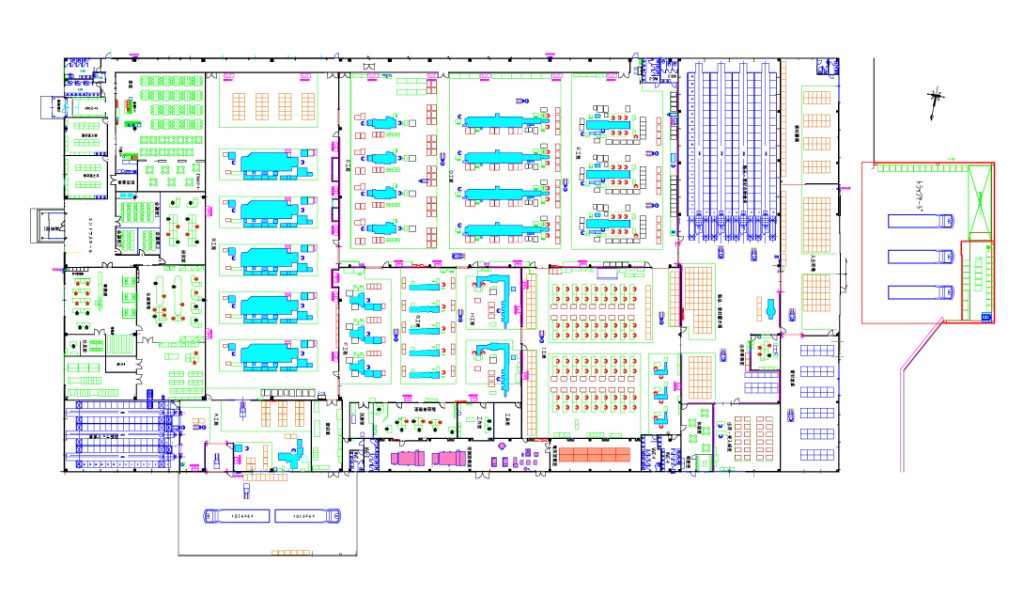
詳細レイアウト図作成の効果
「でも、細かい図面を描くのには手間も時間もかかり、設計者や担当者の負担が増える」という声があるかもしれません。
確かに、詳細レイアウト図をきちんと作成するためには、各機械メーカーや管理部門、現場リーダーなど多方面との打ち合わせが必要となり、手間はかかります。
しかし、それを省いた結果、実際にレイアウトどおりに機械を設置できなかったり、運用を開始してから作業効率が悪いことに気づいたりすれば、かえって多大なコストや時間が必要になります。
結局、詳細レイアウト図をしっかり作り込むほうが、長い目で見れば大幅にリスクを下げ、作業効率と安全性の向上につながるのです。
次に考慮すべき事
詳細レイアウト図を描くうえでは、機械だけでなく物流動線や作業者の作業効率、在庫管理のしくみ、安全設備など、多岐にわたる要素が絡み合います。
次に把握しておきたいのは、こうした要素をどのように組み合わせながら図面に反映させるか、具体的なツールやソフトウェアを使うときに気をつけるポイントは何か、そして最終的なレイアウト確認から工事に至るまでのチェックリストなどです。
詳細レイアウト図の作成は、工場の稼働を左右する最終段階の重要な工程です。
細かいところまでしっかり描き込むことで、工場計画の完成度が飛躍的に上がります。
逆に、この作業を疎かにすると、余計な修正や手戻りが頻発し、コスト超過や納期遅延につながるリスクを高めます。
工場の稼働率や生産効率を最大化するためにも、時間と労力を惜しまず取り組みたいポイントです。
詳細レイアウト図で押さえるべき重要なポイント
ここでは、詳細レイアウト図を作成するときに意識すべき具体的なポイントをいくつかご紹介します。
1. 物(原料・部品・製品)の流れを再確認
工場内で扱われる物がどのように移動し、変化していくのかを最初に明らかにしましょう。工程ごとの入出庫量やサイクルタイムを見込み、想定外のボトルネックが発生しないようにします。
必要ならばストックポイントや作業余力を再度検討し、詳細レイアウト図に反映してください。
2. 人の動きと安全性の確保
人の安全確保は、工場運営の基本中の基本です。
作業者の動線(ウォーキング・ライン)が交差しないことや、重い物を運搬する際に無理な姿勢にならないかなど、人が働きやすいレイアウトかをチェックしましょう。
安全柵や安全マット、警告看板の位置なども詳細図で示すと、実際の運用で安全が担保しやすくなります。
3. 車両や搬送機器の通路計画
フォークリフトやAGV(自動搬送車)などの搬送機器を使う場合、通路の幅や旋回スペース、停止位置を正確に描くことが必須です。
車両の特性や積載物の大きさ、カゴ台車の有無など、細かい点を考慮しながらレイアウトしなければ、通路が狭すぎたり曲がり角を曲がれなかったりします。
事故を未然に防ぐためにも、詳細レイアウト図で通路の規格をしっかり決めましょう。
4. 配管・配線・インフラ設備のレイアウト
工場内に必要な電気、空圧、排気、給排水などのインフラの配置も重要です。
どこにコンセントやバルブ類を配置するか、早い段階で決めておかないと、後から配線が足りず延長コードを引き回すような非効率につながりかねません。
省エネやメンテナンスの面でも設計段階で適切に計画し、詳細レイアウト図に盛り込みます。
5. 拡張や変更を見据えた柔軟性
将来的に生産量が増加したり、新しい製品ラインを追加したりする可能性がある場合には、詳細レイアウト図の段階で拡張性を確保しておきましょう。
余白スペースやレイアウト変更が容易なユニット化など、未来の生産変化に対応できる設計にすることで、長期的なコスト削減と効率維持につながります。
ベネフィットと未来の展望
詳細レイアウト図をしっかり作成することで得られるベネフィットは大きく、将来への投資といえます。以下にその主な例を挙げます。
1) 生産性の向上
細部まで無理・ムダ・ムラのないレイアウトを組むことで、手待ちの時間や工程間のロスが減り、全体的な生産性が上がります。
2) 作業者の安全と快適さ
通路幅を確保し、安全設備を適切に配置することで、労働災害のリスクが減少し、作業者にとっても働きやすい環境が整います。
これは企業としての信頼性やブランドイメージ向上にもつながります。
3) 設備投資の最適化
レイアウト決定後に、「やっぱり場所が合わないから新しい機械は入れられない」といった事態を防ぐことで、将来の追加投資を抑えながら設備導入計画を進められます。
4) 将来の変更や拡張にも柔軟に対応
詳細レイアウト図の段階でレイアウト変更の余地を残しておけば、生産量が増加したときや新製品ラインを導入したいときに、スムーズに対応できます。
これにより、変化の激しい市場環境でも企業の競争力を維持しやすくなります。
こうした未来を見据えた詳細レイアウト図を作成することで、最終的には工場全体のコスト削減と生産効率の向上、さらには経営者や顧客からの信頼向上につながっていくのです。
まとめ:
基本レイアウト案をもとに、さらに細かい部分まで検討を加えることで、実際の稼働に耐えうる工場計画が完成します。
詳細レイアウト図を疎かにすると、現場で数多くの不具合が発生し、それらを解決するためのコストや時間がかさんでしまいます。
逆に、綿密な詳細レイアウト図を描ければ、スムーズな工場立ち上げが可能になり、後々の運用でも効率と安全性を高いレベルで維持できます。
今回は、詳細レイアウト図を作成する際に考慮すべきポイントやメリットを中心にお伝えしました。
実際に図面を描くときには、CADソフトや製造シミュレーションソフトを使う場面も多いでしょう。
その際には、現場担当者や設備メーカーとの打ち合わせを密にし、情報を正確に集めることが欠かせません。
また、詳細レイアウト図を完成させた後でも、工事が始まる段階で気づくことや設計変更が生じる可能性はあります。
そういった問題に柔軟に対応しつつ、より良いレイアウトを追求する姿勢が大切です。
可能であれば、詳細レイアウト図に参考となる写真やイメージを挿入したり、実機のサイズ感を共有できるような3Dモデルを活用したりするのもよい方法です。
視覚的な情報が増えるほど、現場の理解度が上がり、意図せぬトラブルが軽減されます。
今後は、詳細レイアウト図をどのように管理・更新していくかが新たなテーマとなりえます。
工場は生き物のように変化していくので、定期的に見直しやメンテナンスを行い、最適な状態を長く維持することが重要です。
参考
工場の新設や拡張や模様替えで、工場のレイアウトを考える必要が出てきた場合、まずは、下記の「やさしい工場レイアウト手法」のメール講座がおすすめです。
無料ですので、ぜひ活用してみてください。
➡︎ 【無料】『やさしい工場レイアウト手法』メール講座