工場レイアウト設計 ― 未来の工場を目指すブロックレイアウト図作成方法
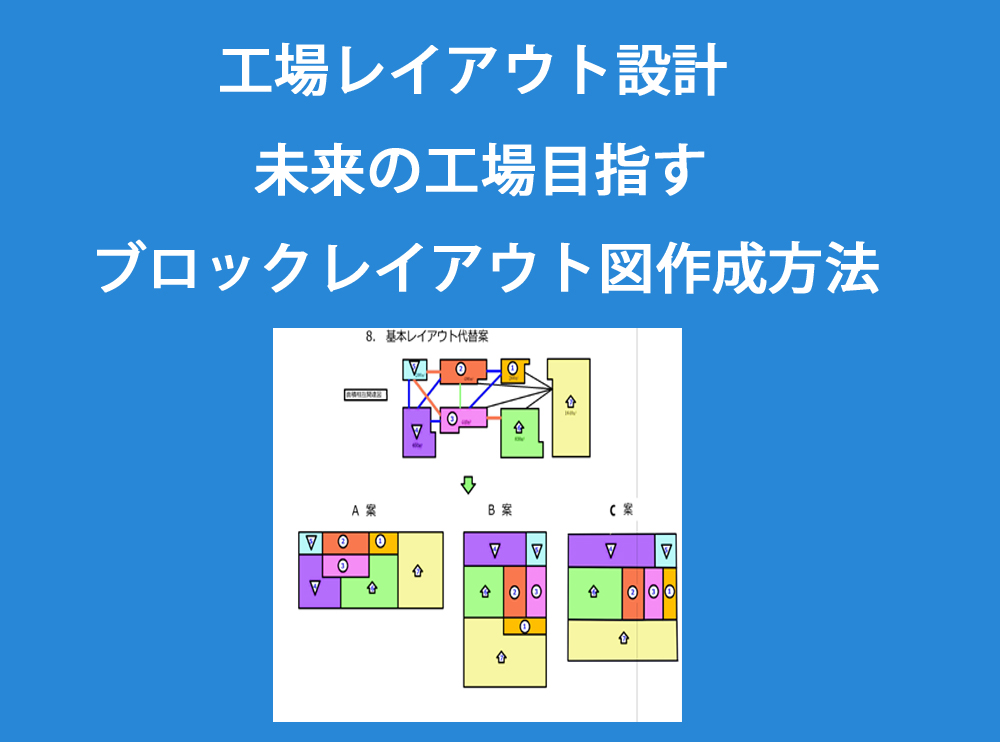
目次
要約
工場のレイアウト設計は、工場全体の効率性、安全性、そしてコスト削減を可能にする最も重要なプロセスの一つです。
その中でも「ブロックレイアウト図」は、設計全体の基盤となり、成功の鍵を握るステップとなります。
この記事の目的
この記事では、以下のような悩みを抱えている方々に向けた解決策を提供します:
・どのように工場レイアウト設計を始めれば良いかわからない初心者の方。
・効率的で実用的な工場レイアウト設計の手順を知りたい方。
・失敗を避け、確実に成果を出したい方。
これを読むことで、以下のような成果が得られるでしょう:
1. 効率的で成功するための工場レイアウト設計プロセスを深く理解できます。
2. 設計における一般的な失敗を防ぐための具体的な戦略を学べます。
3. 遅延や停滞している設計プロジェクトを前進させる明確な方法を身に付けられます。
(既に工場レイアウト検討を始め、停滞中の人)
私はこれまでに計11棟の工場や倉庫のレイアウト設計に携わり、経験から得た知識と実践的な洞察をもとに、この情報を詳細に解説します。
「工場レイアウト設計」における「ブロックレイアウト図作成」の位置付け
「ブロックレイアウト図作成」は工場レイアウト設計の設計段階の6番目ステップの重要な手順に位置します。
この手順は、全体の設計プロセスの骨格を形成し、プロジェクト全体を具現化するための中心的な役割を果たします。
その位置を次図に示します。
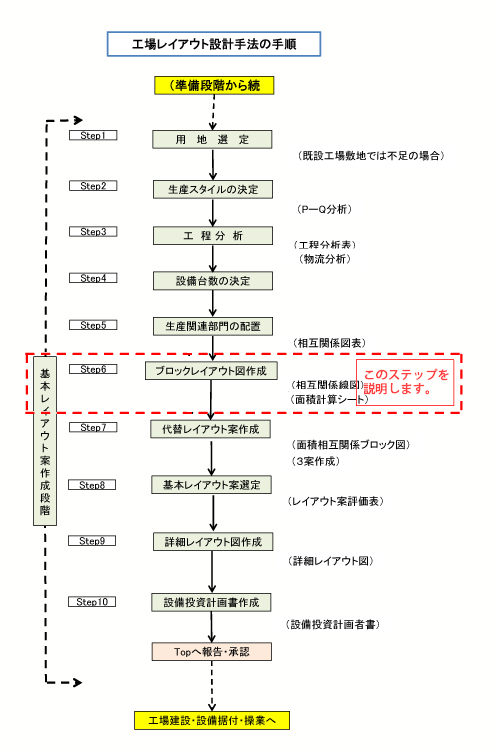
設計プロセスの詳細
以下は工場レイアウト設計の主要なプロセスです:
- 目標設定
設計の目的や目標を明確にすることが最初のステップです。
目標設定では、工場が目指すべき効率化の基準や生産性の目標、さらに従業員の安全確保やコスト最適化を具体的に定めます。
この段階が曖昧であれば、後の工程がぶれる原因となるため慎重に行う必要があります。
- データ収集
必要な情報を収集し、詳細に分析します。
これには、現在の製造工程のデータや物流情報、製品仕様、従業員数、工場敷地の詳細などが含まれます。
収集したデータは、後の設計段階での意思決定を支える重要な基盤です。 - 制約条件の確認
工場の物理的な条件や法規制を確認します。
敷地面積、環境法規制、地域の規制、そして既存の設備状況など、具体的な制約条件を把握し、それらを考慮した設計案を構築します。 - 基本設計
基本的なレイアウトの初期案を作成します。
この段階では、配置の大枠を検討し、生産効率、安全性、コスト削減の観点から評価を行います。 - 部門面積の算出
各部門に必要なスペースを計算します。
製造部門、物流部門、倉庫、事務所など、それぞれが必要とする面積を割り当てることで、全体のスペースの有効活用を図ります。 - ブロックレイアウト図作成
レイアウトの骨格となる図面を作成します。
これにより、物理的な配置が具体化され、設計案の現実性が高まります。
ブロックレイアウトは後の詳細設計を進めるための基盤として機能します。 - 詳細設計
作成されたブロックレイアウトを精密化し、詳細な設計案を完成させます。
これには、各設備の具体的な配置や動線の設計、安全対策の組み込みが含まれます。 - 最終調整と導入
設計案を現場で検討し、必要に応じて最終調整を行います。
この段階では、現場での問題点をフィードバックし、設計を微調整します。
ブロックレイアウト図の作成はこれらのステップの中で、設計プロセス全体の骨格を支える工程です。
この工程を正確に遂行することで、後の詳細設計がよりスムーズに進むことになります。
ブロックレイアウト図作成の重要性
ブロックレイアウト図の作成が工場設計において重要である理由は以下の通りです:
1. 生産効率の向上
適切に設計されたブロックレイアウト図は、作業者の移動距離を短縮し、工程間の作業フローをスムーズにします。
この結果、無駄を最小限に抑えることができ、生産効率を飛躍的に向上させます。
2. 安全性の確保
機械や設備の配置を最適化することで、危険区域を明確化し、安全な動線を確保します。
これにより、労働災害を未然に防ぎ、従業員が安心して業務を行える環境を整えます。
3. コスト削減
スペース利用の効率化により、運搬コストや設備投資費用を削減できます。
さらに、設計段階での問題点を事前に解決することで、後工程での修正コストを最小化できます。
4. 環境への配慮
効率的なレイアウト設計は、資源の無駄遣いを減少させ、環境負荷を軽減する可能性があります。
例えば、移動距離の短縮によりエネルギー消費を抑えることができ、持続可能な工場運営に寄与します。
これらのメリットは、効率性や生産性の向上だけでなく、工場全体の長期的な利益に直結します。
ブロックレイアウト案図の作成の手順
工場レイアウト設計におけるブロックレイアウト案図作成のプロセスは、非常に重要で細心の注意を要する工程です。
以下は、ブロックレイアウト図を作成するための具体的な手順です
1. 必要面積の算出
まず、機器や設備に必要な面積を正確に算出します。
これにより、各設備が占有するスペースや作業スペースが明確になります。
具体的には以下の情報をデータとしてまとめる必要があります:
- 機器・設備の寸法:
各機器の正確なサイズを確認し、専用データ用紙に記入します。 - 物流通路や作業スペース:
作業者の動線を確保するための通路幅や安全スペース。 - 保管エリアの必要面積:
材料や製品の保管に必要なスペース。
また、設備や機器の仕様をデータベース化して管理することで効率化を図ります。
給排水やエネルギー関連の仕様は、将来的なレイアウト変更や実施段階で重要な役割を果たします。
機器・設備の寸法は、次図のような設備データ用紙に記入します。
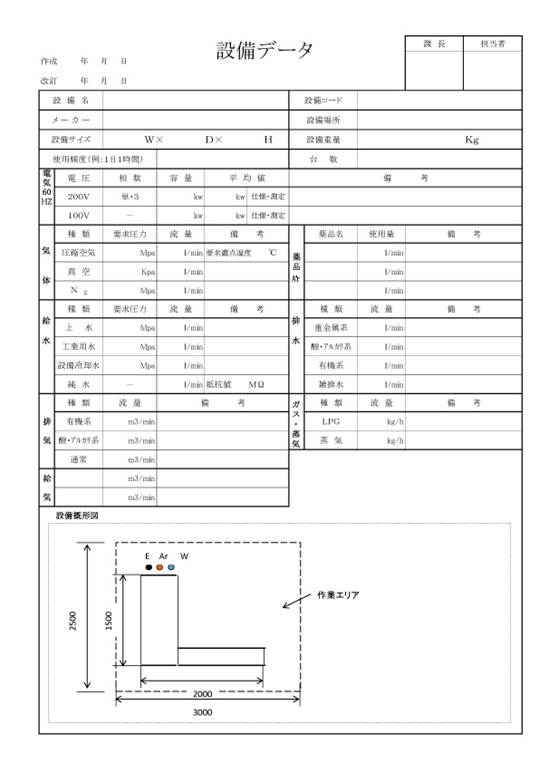
各エネルギー、給排水の仕様は、レイアウト変更の実施段階で必要になってきます。
この資料を基に、各工程の部分詳細レイアウト図を作成し、必要面積を算出します。
部分詳細レイアウトの事例です。
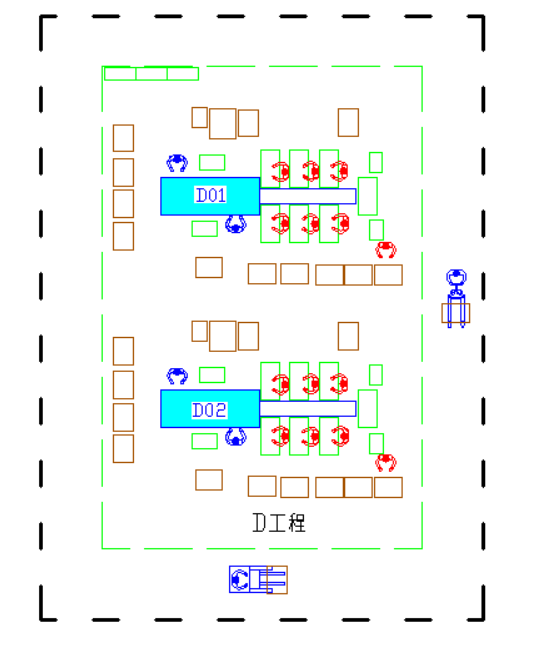
生産設備、作業者配置、作業エリア、仕掛品、完成品、副資材、部品棚、通路等を配置した詳細レイアウトを書いて、必要面積を算出します。
後の設計作業で工場全体詳細レイアウト図を作成する場合、この各工程の部分詳細レイアウト図のデータを合成して書きます。
2. 面積データの集計
次に、各生産部門の必要面積をリスト化し、面積計算シートに記録します。
このシートは、後のブロック配置の基準となるため、細心の注意を払って正確に作成することが重要です。
例えば、部門ごとの生産スペースや物流エリアを明確に分割し、それぞれの必要面積を算出します。
次図のような面積計算シートに記録します。
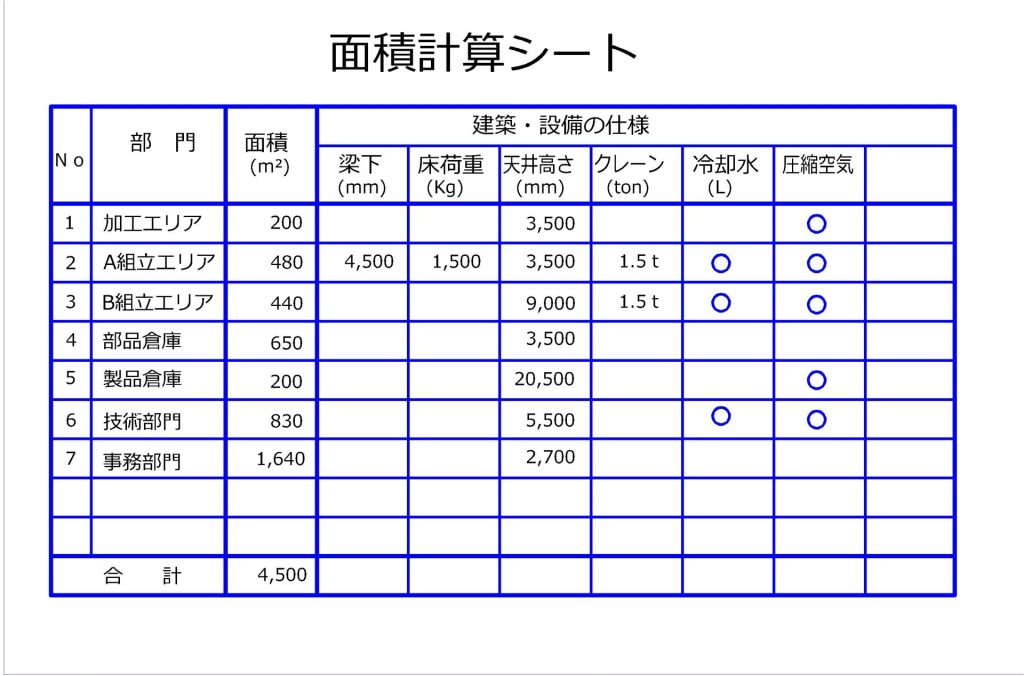
3. ブロックの配置
算出された各部門の面積をブロック化し、相互関連図の位置に配置します。
この工程では、部門間の連携や物流の効率性を考慮して、ブロックを配置します。
完成した面積相互関連図を基に、作業の流れが途切れることなく連携が維持される配置を設計します。
完成した面積相互関連図を次図に示します。
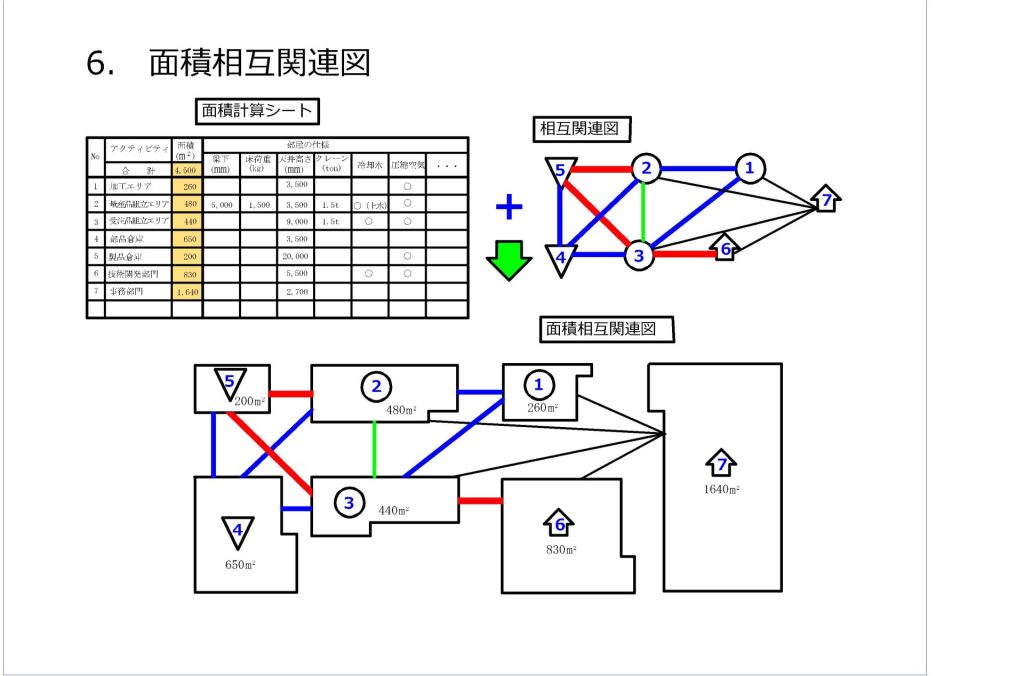
これで、工場レイアウトの基礎となるブロックレイアウト図か作成できます。
成功事例
適切なブロックレイアウト図の設計は、実際に多くの成果をもたらしています。
以下は過去の成功事例です:
作業効率の向上
過去の成功事例として、ある工場では動線設計を改善したことで作業効率が30%向上しました。
同じリソースでより多くの成果を上げることができました。
コスト削減
別の事例では、スペース配分を最適化することで年間コストが15%削減されました。
特に物流効率の向上が大きな効果を発揮しました。
プロジェクト期間の短縮
設計段階で正確な計画を立てることで、プロジェクト全体の期間を20%短縮することができました。
これにより、早期の稼働開始が可能となり、収益向上に寄与しました。
ブロックレイアウト案図の作成のまとめ
ブロックレイアウト図の作成は、効率的な工場設計を実現するための不可欠なステップです。
設計プロセスのどの段階でも重要なのは、現実に即した設計を行うことです。
理想的な効率性や安全性を追求する一方で、実際の現場での課題や制約を踏まえた計画を立てることが求められます。
特にブロックレイアウト図の作成段階では、現実的な目標設定、データの正確な分析、そして柔軟性のある設計思想が成功を導く鍵となります。
参考
工場の新設や拡張や模様替えで、工場のレイアウトを考える必要が出てきた場合、まずは、下記の「やさしい工場レイアウト手法」のメール講座がおすすめです。
無料ですので、ぜひ活用してみてください。