工場レイアウト設計成功のための効果的な現状分析手法
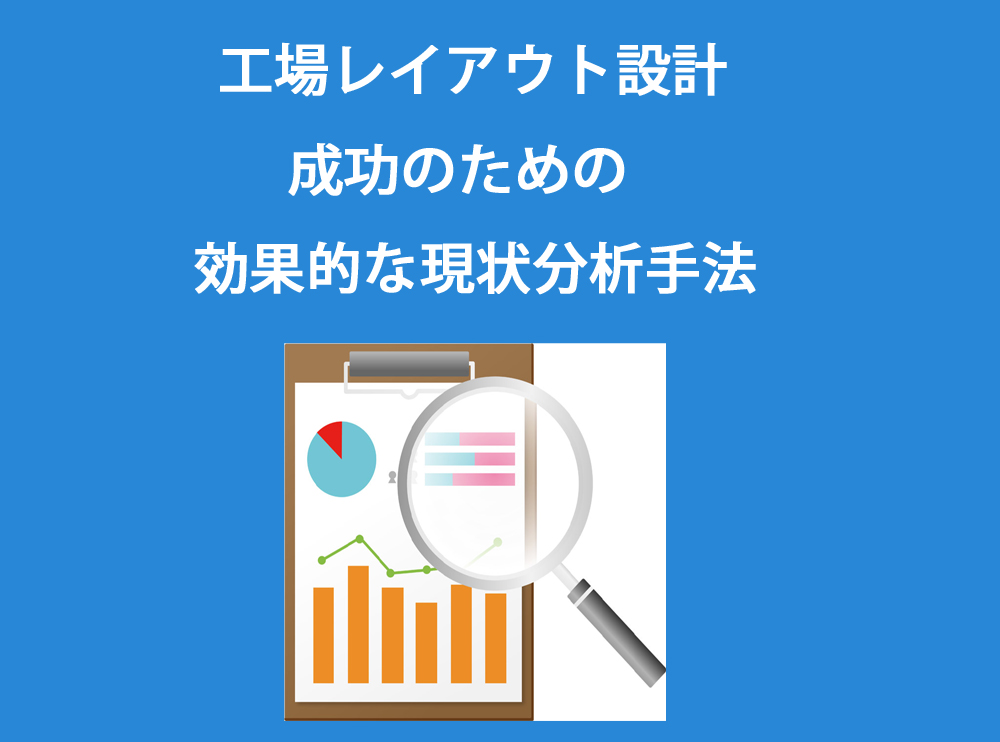
工場レイアウト設計成功のための効果的な現状分析手法
目次
要約
工場レイアウト設計における現状分析は、効果的な生産プロセスの確立や効率の向上に不可欠なステップです。
この記事では、現状分析の重要性と効果的な手法について解説します。
この記事は、
*はじめて工場レイアウト設計の担当者になったが 、なにから始めたらよいのかわからないんです…
*工場レイアウト設計は、現状分析の方法が分からず、とても不安です…
*工場レイアウト設計の実践的で確実な手法の手順を教えてほしい!
といったような方へ向けてまとめています。
この記事を読むことで、
*工場レイアウトの設計で成功するための重要なパターンやポイントを全て知ることになります。
*工場レイアウト設計の失敗を事前に回避できます。
*足踏み状態から前進していくことができます。(既に工場レイアウト検討を始め、停滞中の人)
私はこれまで計11棟の工場や倉庫のレイアウト設計に携わってきました。
その過程で知り得た工場レイアウトの設計などを説明していきたいと思います。
どうぞ、よろしくお願いします!
「工場レイアウト設計」手順における現状分析の位置
「工場レイアウト設計」における「現状分析」の手順は、生産規模の決定の次になります。
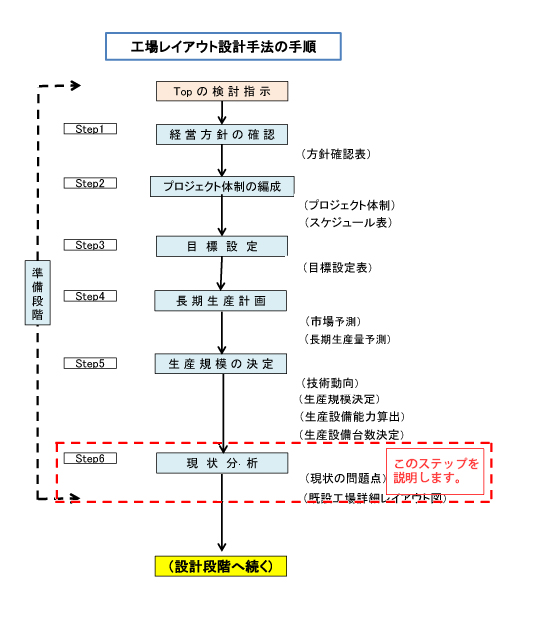
現状分析の重要性
現状分析は、工場の構造、プロセス、設備、人員配置など、すべての要素を評価するための基盤です。
現状を正確に把握することで、問題点や改善の余地を特定し、効果的な改善策を立案することができます。
また、顧客ニーズや市場動向に合わせて工場を最適化するためには、現状の把握が不可欠です。
現状分析の手法
フローチャートやプロセスマップの作成
工場内の生産プロセスを可視化し、問題点を特定します。
5S活動の実施
整理整頓、清掃、清潔、清潔、規律の5つの原則に基づいて、現場の改善を促進します。
(詳しくは5S活動のアイデアをご覧ください。)
工場詳細レイアウト図
工場内の配置やレイアウトを詳細レイアウト図にして、効率的な動線を確保します。
データ分析
生産データや労働力の活用状況などのデータを分析し、問題を発見します。
現状分析の手順
目的設定
分析の目的を明確にし、重点項目を設定します。
データ収集
工場内の各種データを収集し、必要な情報を整理します。
分析と評価
収集したデータを分析し、問題点や改善の機会を特定します。
提案と改善計画の策定
問題点に対する具体的な改善策を立案し、改善計画を策定します。
現状分析の検討項目
チェックリストの作成
現状分析の検討項目は広範囲に渡るため、チェック漏れがないように次の様なチェックリストを用意します。
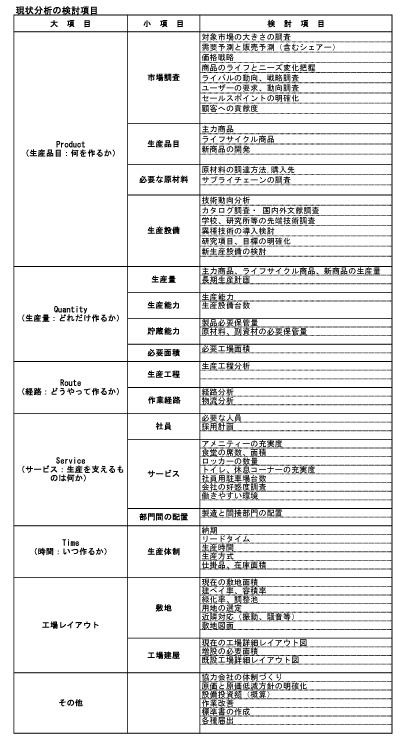
チェックリストの検討項目の説明
Product(生産品目:何を作るか)
市場調査
対象市場の大きさの調査
需要予測と販売予測(含むシェアー)
価格戦略
商品のライフとニーズ変化把握
ライバルの動向、戦略調査
ユーザーの要求、動向調査
セールスポイントの明確化
顧客への貢献度
生産品目
主力商品
ライフサイクル商品
新商品の開発
必要な原材
原材料の調達方法,購入先
サプライチェーンの調査
生産設備
技術動向分析
カタログ調査・ 国内外文献調査
学校、研究所等の先端技術調査
異種技術の導入検討
研究項目、目標の明確化
新生産設備の検討
Quantity(生産量:どれだけ作るか)
生産量
主力商品、ライフサイクル商品、新商品の生産量
長期生産計画
生産能力
生産能力
生産設備台数
貯蔵能力
製品必要保管量
原材料、副資材の必要保管量
必要面積
必要工場面積
Route(経路:どうやって作るか)
生産工程
生産工程分析
作業経路
経路分析
物流分析
Service(サービス:生産を支えるものは何か)
社員
必要な人員
採用計画
サービス
アメニティーの充実度
食堂の席数、面積
ロッカーの数量
トイレ、休息コーナーの充実度
社員用駐車場台数
会社の好感度調査
部門間の配置
製造と間接部門の配置
Time :(いつ作るか)
" 生産体制
納期
リードタイム
生産時間
生産方式
仕掛品、在庫面積
工場レイアウト
敷地
現在の敷地面積
建ペイ率、容積率
緑化率、調整池
用地の選定
近隣対応(振動、騒音等)
敷地図面
工場建屋
現在の工場詳細レイアウト図
増設の必要面積
既設工場詳細レイアウト図
その他
協力会社の体制づくり
原価と原価低減方針の明確化
設備投資額(概算)
作業改善
標準書の作成
各種届出
工場詳細レイアウト図例
現状の工場レイアウト図は、情報を可視化して詳細レイアウト図にする必要があります。
次図がその例です。
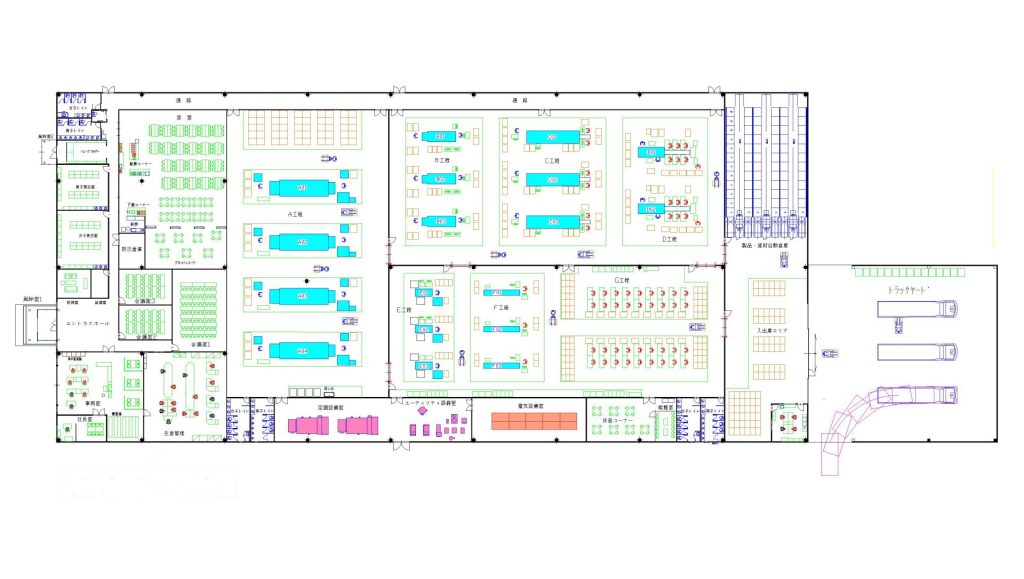
まとめ
要約
工場レイアウト設計における現状分析は、生産プロセスの効率化や改善において極めて重要な段階です。
本記事では、現状分析の重要性とその効果的な手法について詳しく解説します。
現状分析の重要性
現状分析は、工場の構造、プロセス、設備、人員配置など、あらゆる要素を評価するための基盤となります。
正確な現状把握により、問題点や改善のポイントを特定し、効果的な改善策を策定することが可能となります。
また、市場ニーズや競合状況に合わせて工場を最適化するためにも、現状分析は不可欠です。
現状分析の手法
フローチャートや詳細レイアウト図の作成:
工場内の生産プロセスを視覚化し、問題点を特定します。
5S活動の実施:
整理整頓、清掃、清潔、清潔、規律の5つの原則に基づき、現場の改善を促進します。
レイアウトマッピング:
工場内の配置やレイアウトをマップ上に図示し、効率的な動線を確保します。
データ分析:
生産データや労働力の利用状況などのデータを分析し、問題点を発見します。
現状分析の手順
目的設定:
分析の目的を明確にし、重点項目を設定します。
データ収集:
工場内の各種データを収集し、必要な情報を整理します。 分析と評価: 収集したデータを分析し、問題点や改善の機会を特定します。
提案と改善計画の策定:
問題点に対する具体的な改善策を立案し、改善計画を策定します。
現状分析の検討項目:
チェックリストの作成
工場の構造、設備、人員配置などの項目を含むチェックリストを用意します。
参考
「工場レイアウト」設計を支えてくれる「 やさしい工場レイアウト手法」講座(無料のメール講座)でその基本を学んでみませんか?
受講後は、特典や有益な情報を配信しているメルマガも受け取れるようになります。
(購読解除はワンクリックでいつでもできます)。
詳しくは下記のリンクからご覧ください。
『やさしい工場レイアウト手法』メール講座【無料】(5つの特典つき)※初心者向け 〜今すぐに、最適な工場レイアウト案作成が始められる方法〜